
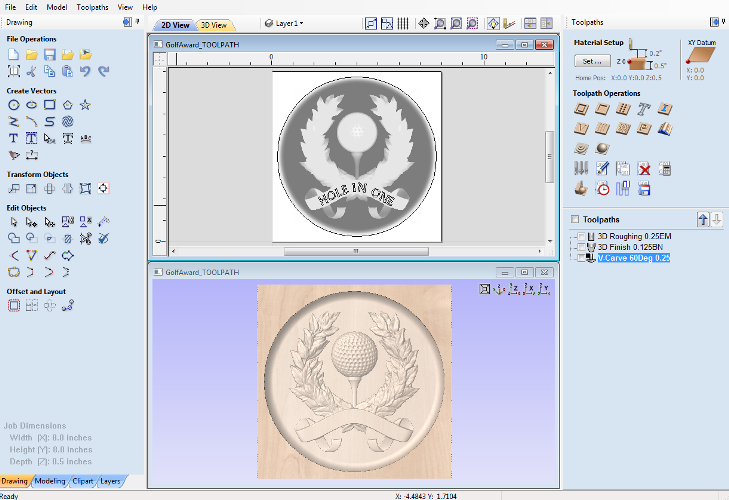
When I do use the recoil, I usually cut them using 2 or 4 sided cuts rather than continuous indexing cuts. Quicker than cutting them one at a time on the recoil. I set up a jig to hold all 4 legs at once, then I can cut the first side on all 4, flip them all, and cut the second side.
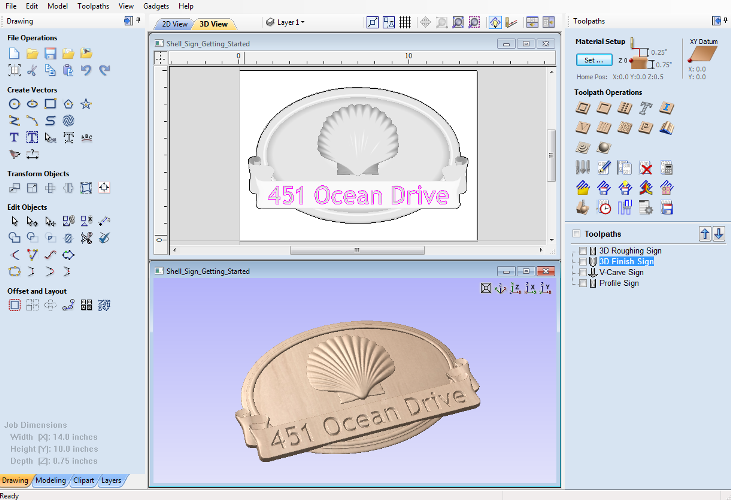
Just for your information, I've ALWAYS found it quicker to machine my legs with 2 sided cuts rather than using the recoil. But if I take my model straight from Rhino and toolpath with MadCAM (integrated with Rhino) they come out fine. The final product, when carved on my recoil, ALWAYS has some distortion. I have had no luck unwrapping 3D furniture legs that have curves in them. To do this on your recoil indexer, I think you would need to design and toolpath it in another program.

You would have to cut the leg with 2 sided cuts, and form the opposite curves for the back side cut (indexing the leg so you can flip it over to cut the back side). To do this, you'd first create the curve in the Z-direction with a 2 rail sweep on a rectangular area, then draw the vectors for the curved leg in the X-Y plane and create a second 2 rail sweep that is added to the first one. You could design a leg that curves in 2 planes by have one curve in the X-Y plane, and the second plane curve in the Z direction. Steve's way will work without the waste from cutting that leg out of such a thick piece of stock. You could do it without attacking from the angle but you would need two different 3d profiles for the two sided machining and you'd have to work with thicker stock and longer bits. Steve's suggestion will work and would probably be the easiest way to wrap your head around. But, yes, it seems easier to do this without the rotary. I had stumbled upon that approach, but needed an STL and wasn't finding the ideal way to model the leg in order to create an STL that could be unwrapped. Thanks for the pointer to the rotary approach of unwrapping an STL model. dealguy's suggestion to rotate the model 45 degrees and mill from the corner of the leg rather than the surface looks quite creative and workable. and I've not been able to find a way to do that. In XYZ, I think it would curve in the X and the Z directions. My example is square, but that's not important) that curves out at the bottom both to the front and the side of the table. However, I'd like the bottom of the leg to curve up/out using the same curves as those used in the two rail sweep.
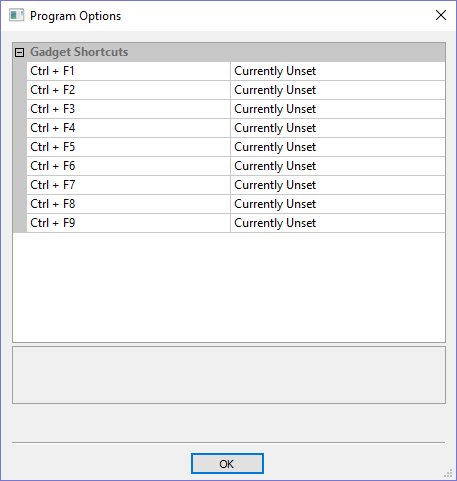
It is quite easy to misunderstand my badly worded question. Frankly, you will get a better result on this kind of leg with 2 sided cutting on the table. There are some kluges you can do to get around this but I will not describe them here. With either approach, if the leg is very wide, you will run into vibration issues and may also have issues with bit length. If it isn't, it creates an ambiguous model in Aspire that will not render or cut properly. The biggest drawback with this method is that the center line of the leg has to be completely enclosed in the part (which it would not be in the example shown here). A harder way is to paste two halves together and then unwrap the resulting model (this can all be done from Aspire). The easiest way is to cut one side as shown in the picture, manually enter g-code to flip the part 180 degrees and reset the rotary to zero, and then cut the other side. The pictures below should give you an idea of what I mean.Īs far as doing these on the rotary, that is a challenge. In other words, your rails will define the curve and the sweep vector(s) will be one or more angles. This can be done, but you need to model it so that one of the corners are on the top.
